In the industrial landscape, especially in regions subjected to harsh cold environments, maintaining the functionality of pipelines, tanks, and various systems becomes a significant challenge. One extremely effective solution for this issue is heat tracing. G & R Insulating, a beacon of excellence in Western Canada’s oil and gas sector, deeply understands the importance and necessity of heat tracing. Explore why heat tracing is crucial for safety, efficiency, and reliability in critical settings in our latest blog post.
Understanding Trace Heating
Heat tracing or heating is applied to maintain or increase the temperature levels of pipes, tanks, and vessels. This process typically uses electric heating cables attached to the pipeline and controlled via a thermostat to regulate temperature accurately. Sometimes, steam trace heating is also utilized, which uses steam lines in contact with the object requiring heat.
Preventing Freezing in Cold Climates
The main reason for trace heating is to avoid the freezing of liquids in pipelines. In Western Canada, temperatures sometimes drop very much making it dangerous for the flow of liquids through pipelines and tanks. When liquids freeze, they expand hence creating points of pressure that may cause pipeline ruptures leading to harmful spills, expensive maintenance, and operational stoppages. This is why we use trace heating. Human-like Text: Most liquid pipelines are laid underground to protect them from the elements like air, rocks, surface water, and many others. Underground pipelines are also safer than aboveground ones. This is because transporting gases via them is less risky as far as explosions and fires are concerned among. Heat tracing systems are well designed in a bid to maintain fluids at a specified temperature for convenience. May include a heat-producing cable encased in an outer protective plastic sheathing having an insulation material provided with current conducting wire wrapped around said core covered by an inner plastic layer filled with capillus roots wound around the core. As among the principal distinguishing
Maintaining Optimal Viscosity
The main reason for trace heating is to avoid the freezing of liquids in pipelines. In Western Canada, temperatures sometimes drop very much making it dangerous for the flow of liquids through pipelines and tanks. When liquids freeze, they expand hence creating points of pressure that may cause pipeline ruptures leading to harmful spills, expensive maintenance, and operational stoppages. This is why we use trace heating. Human-like Text: Most liquid pipelines are laid underground to protect them from the elements like air, rocks, surface water, and many others. Underground pipelines are also safer than aboveground ones. This is because transporting gases via them is less risky as far as explosions and fires are concerned. Heat tracing systems are well designed in a bid to maintain fluids at a specified temperature for convenience. The design may consist of a heat-producing cable encased in a protective plastic sheathing, with an insulation material and current conducting wire wrapped around the core. Inside, an inner plastic layer contains capillus roots wound around the core, enhancing its structure.
Enhancing System Reliability and Safety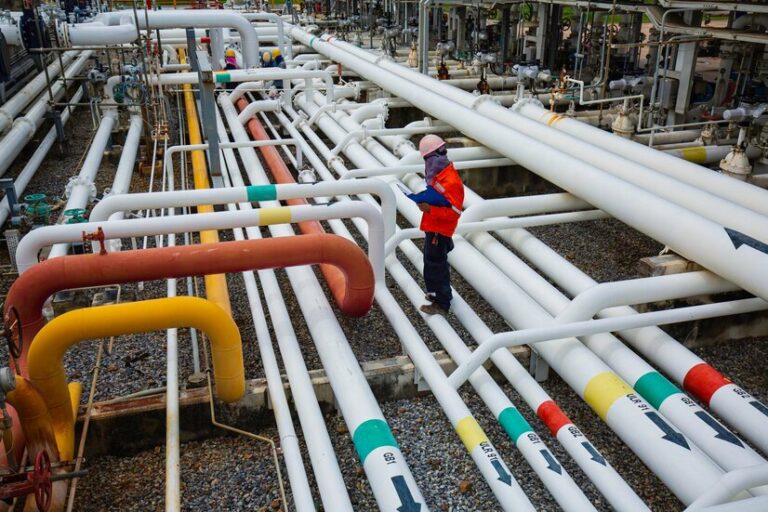
The proper viscosity is crucial for efficient movement and treatment of fluids in the oil and gas industry. Some fluids like crude oil can turn into high viscosity or solidify under low temperatures. Those liquids should keep their right viscosity if transportation and maintenance of flow are to be maintained without interruption. Such temperatures could cause the above things to happen on certain liquids at times in any form or shape except for solidification. Because they are used to keep liquid crude moving at constant height requiring no pumping power. Therefore, it is clear from this perspective why many pipelines handling this type of substance may need heating mechanisms that serve almost no other purpose except perhaps for oil. Such a purpose is achieved through the installation of electrically powered trace heating systems. Their primary work is to maintain the fluidity of the oil within them to prevent any possible harm that may result from congealed forms of the same. Therefore, these gadgets are important because they keep it flowing just like water even if it is cold thus restricting penetration of the oil.
Energy Efficiency and Cost-Effectiveness
The early stages required investing substantial amounts of money; however, it is very clear that there is a great deal of energy efficiency and cost-cutting realized over time. Modern-day systems, heat themselves using less energy because they have controls that direct this heat more efficiently. Emergency breakdowns are minimized when pipes don’t freeze or oil stays thin, ensuring a continuous flow. Viscosity maintenance leads to considerable periods without production stoppage.
Compliance With Industry Standards and Regulations
In many regions, stringent regulatory standards concerning operational safety and the environmental impact of the oil and gas industry are put in place. Trace heating plays a crucial role in enabling companies like G & R Insulating to meet these regulations effectively. By implementing trace heating solutions, pipelines and fluid transport systems can operate safely and efficiently, minimizing the risk of accidents and environmental harm. This not only helps companies remain compliant with regulations but also contributes to overall industry sustainability and responsible resource management. Ensuring that fluids do not freeze and maintaining optimal flow reduces the likelihood of spills and other environmental hazards. This, in turn, upholds regulatory compliance and avoids potential fines and legal complications.
Applications Beyond Oil and Gas
Trace heating has several uses in certain industries like the oil and gas sector. The quality and stability of products in the chemical and food processing areas depend on the maintenance of precise temperatures. Chemical solutions, syrups, and other substances whose temperatures can easily be affected use heating systems to maintain their favorable temperatures. These systems are used both in homes and businesses.
Choosing The Right Trace Heating System
It’s important to choose the right system for performance to be at its best. There are several things one needs to think about including specific application. Temperature maintenance desired, whether it is hazardous or not, and size of pipes in length & diameter. Electric heating systems are highly customizable and offer precise temperature control, making them suitable for a wide range of applications. Steam heating, although less common, is effective in specific industrial settings where steam lines are already present.
Installation and Maintenance
For the efficient and durable functioning of electric heat-tracing systems, correct installation and maintenance should be carried out. When we install projects at G & R Insulating Company we prioritize rigorous quality control procedures together with safety measures. This is done through thorough inspection and testing making sure that the system complies with necessary standards. It is also important that the system be regularly maintained. This will help in identifying anything that might potentially go wrong. For example, insulation breakages or problems with the thermostat that would affect its performance.
Future Trends in Trace Heating
Increased technology guarantees the development of warming systems that keep advancing and offer improved productivity and dependability. More common are new concepts like self-regulating heating wires. These can automatically adjust to temperature changes between cold and hot environments. They are now used for efficient power utilization, thus reducing the chances of
high-temperature conditioning that may interfere with operations at any given time. Moreover, including IoT (Internet of Things) technology means that remote monitoring and control of trace heating systems can be done.
Case Study: Trace Heating in Action
Imagine a real-world situation in which a G & R Insulating Company installed specialized heating systems in an oilfield in Alberta. Winters in Alberta’s oilfields are extremely cold, posing a risk of fluid flow in the pipes being blocked due to freezing. Over the years, this has been a recurring issue due to the consistently low temperatures. This necessitated a customized electric heating system that was designed in such a way that it maintained the required temperatures to prevent freezing. Thus allowing for uninterrupted operation of the facilities.
Conclusion
Preventing the freezing of fluids in cold climates, maintaining the right viscosity for effective transportation, or ensuring that the system is both reliable and safe are the functions of trace heating. We at G & R Insulating have an intimate knowledge of the vital importance possessed by this technology especially when one delves into the oil and gas industry. Our dedication to the cause means that we have been providing very effective solutions intended for the regulation of such systems over the past twenty years or so. These systems play a major role in not only safeguarding the industry’s operations but also improving sustainability through energy conservation, which besides meeting specific requirements as far as grid management or some other facets are concerned, creates efficient use of resources as well as lowering. If you’re considering investing in these solutions, G & R Insulating is here to provide expert guidance and high-quality options tailored to your specific needs.